TextilE
Finishing
The aim of textile finishing is to complete the production cycle of textiles of various presentations.
In textile finishing, often also referred to as finishing, the textile raw material is made ready for use by means of various processes so that it can be further processed as a textile surface. For example, a preparation or sizing applied during the manufacturing process must be removed, as well as defects and dirt. Furthermore, finishing is used to give textiles properties that they do not naturally possess. Particularly in textile finishing, great importance must be attached to environmental protection, both in terms of waste water and exhaust air. Finishing is always a combination of different operations using chemical, mechanical or chemical-mechanical processes. These can be independent of the raw material, but are often based on the chemical composition and surface properties of the fibers used.
In singeing, protruding fiber ends are burned away by gas flames or other heating elements, resulting in a smooth surface.
Washing processes are necessary both in the pretreatment and in the intermediate and posttreatment stages to remove impurities, preparations, sizing residues, etc. This is done with appropriate washing machines, also called jiggers. After such a wet treatment and before further thermal treatments, the fabric must be dewatered, which is done by spinning, suction or squeezing. It is then dried on the stenter frame. Any warping of the fabric caused by previous operations can be compensated for during the corresponding fabric infeed. For this purpose, the fabric is gripped on both sides with needles or clips and guided through the drying chamber to the desired width.
For synthetic fibers, heat-set is one of the most important finishing processes. Fixing compensates for tensions in the interior of the fiber that have arisen during fiber extraction and processing down to the surface. By heat-treating the thermoplastic synthetic fibers and then cooling them in a controlled manner, the fibers are fixed in a state of least stress. This makes them stable in shape and size.
The calendar plays a special role as a final treatment in textile finishing. It has the task of smoothing textile surfaces, compressing them by pressure and producing a shiny surface. For this purpose, the textile material is passed between rollers that are under pressure and temperature controlled. Depending on the desired effect, the roller properties, temperature, arrangement and speed play an important role.
While the task of dry finishing is essentially to change the surface, wet finishing gives textiles new properties that represent an improvement over the properties of the individual fiber materials. In impregnation, for example, textiles are impregnated or sprayed with water-repellent chemicals. Coating, on the other hand, is the application of synthetic substances to a textile surface with subsequent consolidation, for example on a stenter frame. Coating also creates a textile surface with new properties resulting from the properties of the carrier material and the coating compound. Here, it is important that the plastic surface is porous enough to ensure air and moisture transport. In laminating, two or more textile surfaces can be joined together. This is done by thermal lamination or by an adhesive. The latter also ensures a porous surface.
Arrange a call
Please feel free to send me a message. Either directly by
e-mail or add me to your network on LinkedIn and contact me there. I look forward to meeting you and talking to you about solving your problems.
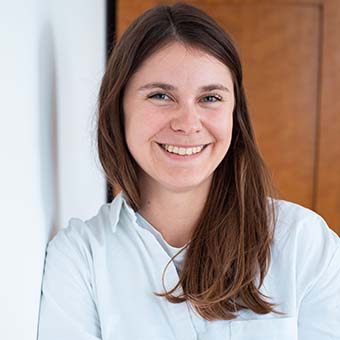
Adress
R+F FilterElements GmbH
Wollenweberstraße 25
31134 Hildesheim
Germany